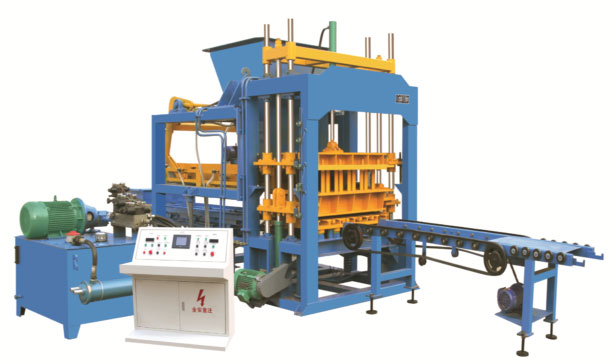
1, The first is to adjust the gap between feeding mechanism scraper and cartridge floor, should not be more than 2 mm, the gap between the underside of the feeding mechanism under the cartridge and the market should be not more than 0.5 mm, the adjustment mechanism of the upper barrel of the feeding mechanism There is a gap of 0.5-1 mm with the feeder tray.
2, Do a good job of adjusting the height of the track, so that after the out of the brick, the mold surface should be higher than the disk 1 mm, allowing the use of thin metal track and bracket surface adjustment, pressure brick body eccentric shaft so that it can press out the required brick.
3, The rotary plate mechanism on the rod, gaskets and crankshaft institutions on the spherical eccentric shaft so that it automatically stuck in the empty trip, the more the distance of not more than 3 mm.
4. Adjust the adjusting nut on the vertical axis so that the bottom plane of the pressure bearing template should be parallel to the plane of the revolving disk and leave a clearance of 1-1.5 mm.
5, Followed by the trial operation of the brick machine equipment, including two sections of air cut and load test, the appearance of the machine before the test should be carried out, tighten the fasteners have not yet fastened, clear the surface of the turntable, horizontal hole and other transmission components Debris, at the same time dealing with lubrication points plus enough lubricants, and then manually move the machine, the turntable revolving 2-3 weeks, after checking the machine to confirm that there is no stuck so far.
6, Empty car test time should not be less than 2 hours, empty car test should be carefully observed bearing temperature, gear meshing, motor temperature rise and lubrication, pay attention to the brick work and track top brick parts of the work conditions After a good pass gradually increase the amount of feeding, the load test, and then check the various parts of the work under the load, the load test of not less than 4 hours.